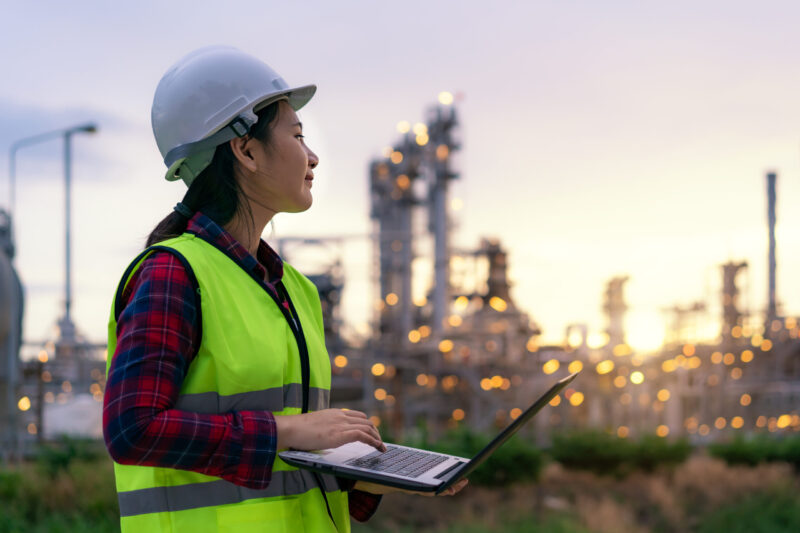
This site
is mobile
responsive
With many countries witnessing rapid growth of the global outsourcing market, Malaysia needs to obtain many more total solutions or manufacturing solution providers in order to secure a larger share, especially for high technology industries. Industry players need to consolidate and realign themselves to provide total solutions to complement the growth of the manufacturing sector in Malaysia, which is moving towards high technology, capital intensive and high value-added industries.
Production planning is a guideline for manufacturers on how to carry out the production process, dealing with basic concepts including what to produce, when to produce, and how much to produce. It is a long-term process that aims to ensure the production effectively; as such, the total manufacturing solutions trend will have a big impact on the industry, by challenging manufacturing companies to manage production more effectively.
Key Elements of a Total Manufacturing Solution
Local companies will have to move towards providing total manufacturing solutions and to enhance their capabilities in order to support the supply chain of the ecosystems within the high technology industries such as semiconductors, aerospace, medical devices, electric vehicles, and photovoltaics.
There are five key elements towards achieve these goals: Industry 4.0 (also known as the Fourth Industrial Revolution @ 4IR); High Technology; Technical Know-How; Knowledge-based Methodologies; and the Upskilling and Reskilling of the Workforce.
Industry 4.0 has changed the global landscape of manufacturing competition by reducing the relative competitive advantage of low-cost regions that rely on cheap labour. Lack of automation systems or Industry 4.0 technologies in manufacturing facilities will hinder a company’s sustainability. Nations and companies that embrace Industry 4.0 technologies and processes will gain over global competitors, as their competitiveness hinges on the ability to transform rapidly in response to market shifts and technology trends.
The impact of advancement and convergence of high technologies are increasingly underpinning global manufacturing competitiveness. Many leading manufacturing players have started to adopt and implement smart manufacturing solutions where advanced hardware is now combined with advanced software, sensors, and data analytics, a move that has resulted in smarter products, processes, and a closer connection between customers and suppliers along the firms’ value chains.
Know-how of technical skills and experiences have become the prerequisite to performing specific tasks. It is this technical know-how which has indirectly strengthened diverse areas of manufacturing, which will capture more market share from global high-tech industries such as semiconductors, electronics, and pharmaceuticals in near future. Among the manufacturing areas that are strengthened include; design and development; manufacturing of high precision metal fabrication components; modules and systems; specialisation of metal surface finishing (such as Black Chrome, Hard Chrome, Flash Chrome, and Anodising and Electroless Nickel plating); and servicing automation multinationals and Local Large Companies (LLCs).
It is also essential that manufacturers make use of their existing knowledge-based manufacturing methodologies to improve their processes by introducing new procedures and tools that support engineers and technologists in facilitating and speeding up their daily work. This result can also be achieved by upgrading their facilities and acquiring technologies to meet the stringent requirements of Original Equipment Manufacturers (OEMs) for parts and components, as well as for precision engineering services.
Finally, there is a need for manufacturers to upskill and reskill their workforce in order to keep up with or even outpace global competitors that have to face the new realities of the global economic environment; this means either hiring more experienced candidates or sending their existing workforce for training to cater for specific needs. The ideal worker will be one who has graduated from local universities that offer courses in Engineering Machining, or from Technical and Vocational Education and Training (TVET) Colleges/Institutes that offer Engineering Diplomas or Malaysian Skills Certificate (SKM) courses.
In fact, there are several collaboration programmes with training institutions including the Penang Skills Development Centre (PSDC), the Walta Centre of Excellence (WCOE), and ViTrox Academy that allow for trained machinists to go through TVET Certification courses that will expose them to daily hands-on experience with sophisticated Computer Numerical Control (CNC) machines and advanced programming, thus enhancing their skills and effectively transforming them into a more highly-skilled workforce.
Encouragingly, two Malaysian companies, Kobay and Penang Automation Cluster Sdn. Bhd. (PAC) have grown through facilitation by MIDA to become a total manufacturing solutions provider. Kobay Technology Bhd, which deals with the aerospace, medical, semiconductor, and solar industries, in addition to related ones effectively upgraded itself into a “One-Stop Centre” for their customers by providing end-to-end manufacturing-related services, including precision machining, surface treatment solutions, fabrication, and assembly.
Similarly, PAC was established to support MNCs and LLCs specifically for E&E industry. It did this by coming up with a bold vision to build and manage the local supply chain ecosystem on advanced, innovative, and cost-effective engineering of sheet metal fabrication, tooling, machining, and metal finishing services with superior quality and delivery packages. The company focuses on the design, development, and manufacturing of high-precision metal fabrication components, modules, and systems.
Facilitation by the Government through MIDA has been actively involved in supporting companies to embrace Industry 4.0 and smart manufacturing technologies to upgrade their manufacturing capabilities through the provision of advice, as well as assistance via grants such as the Industry4WRD Intervention Fund (IIFC) and the Automation Capital Allowance (Automation CA), amongst many other initiatives.
Additionally, MIDA provides for and encourages the adoption of automation and Industry 4.0 technology among machinery and equipment (M&E) industry players through the utilisation of the Automation Project Initiative Platform (API). Last but not least, MIDA has established a Project Acceleration and Coordination Unit (PACU) to facilitate all necessary approvals to ensure projects are implemented in a timely manner.
It is hoped MIDA’s support will result in strong total manufacturing solutions that will support the local manufacturing sector to pave the way towards enhanced productivity, job creation, innovation capacity, the emergence of a high-skilled talent pool, and ultimately economic prosperity and societal well-being. This would position Malaysia as a primary destination for smart manufacturing globally, which will attract more high-tech investments into the country.