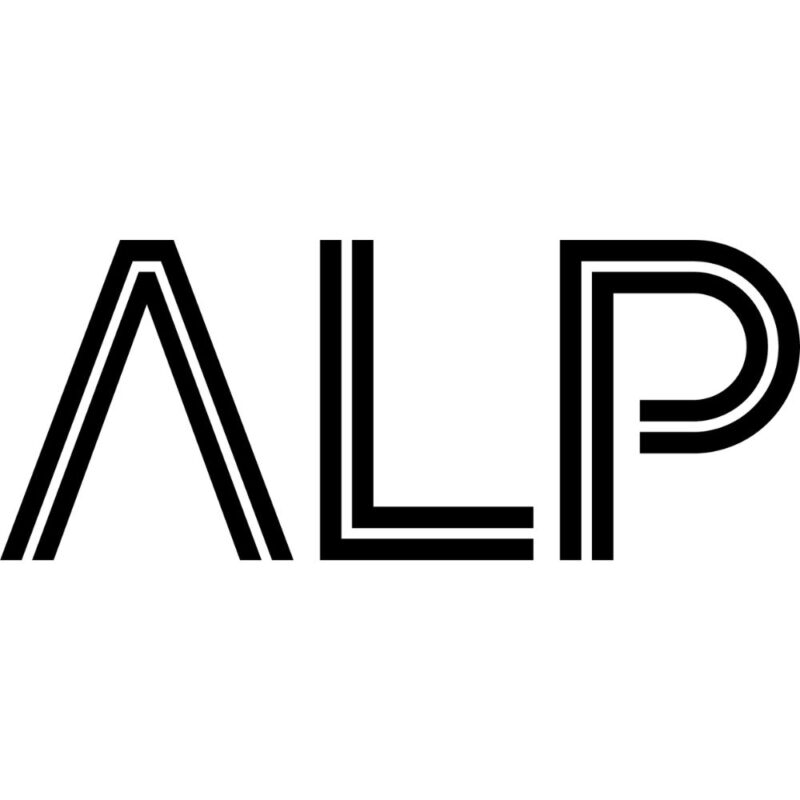
This site
is mobile
responsive
Ally Logistic Property (ALP) is Taiwan’s largest institutional logistics property developer, focused on smart warehousing solutions to digitise the labour-intensive logistics space. Established in 2014, ALP provides cutting-edge smart warehousing solutions, including warehousing property, automation system integration, and warehousing operation planning and optimisation.
With six logistics parks and 14 logistics hubs in Taiwan, ALP now manages more than 570,000 square metres of warehouses and over USD800 million (RM3.5 billion) in assets, while having more than 480,000 square metres of warehouses and over USD650 million assets in its construction pipeline.
By integrating the resources and talents of diverse backgrounds, ALP solves the most complicated logistics processes for its clients and provides them with simpler, smarter, more sustainable solutions through its smart warehouses.
Taiwan, which has long been a global benchmark for technology advancements in the hardware space, was a prime market for which ALP could test and improve its solutions. At the same time, the country’s role as a trading hub made the local logistics space a perfect petri dish for ALP’s solutions to accelerate the digitalisation of labour-intensive supply chains and logistics.
Malaysia as an OMega launchpad for regional aspirations
Having successfully redefined Taiwan’s logistics sector, ALP began its Southeast Asia market expansion in 2019. That same year, the smart warehousing company set up its first subsidiary office in Malaysia. This will be followed by in other neighbouring countries including Vietnam, Thailand, Philippines, and Indonesia.
Its expansion into Malaysia culminated recently with the October 13 launch of ALP’s first OMega international-scale smart warehouse in Bukit Raja, Selangor. OMega is expected to set new standards and inspiration for smart logistics infrastructure.
Charlie Chang, Co-Founder and Chief Executive Officer (CEO) of ALP, said ALP has seen increasing demands for its innovative and future-proof products and services in Southeast Asia.
“With the official announcement and start of construction on this new warehouse facility in Malaysia, ALP is committed to continue driving its effort to spur growth for the industry while empowering local brands in their digital transformation journey to reach new markets and unlock wealth,” he said during the OMega launch ceremony in Bukit Raja.
Also present was ALP Malaysia Managing Director Keren Liu, who believes that the efforts of ALP will revolutionise Malaysia’s warehousing infrastructure through the cutting-edge, integrated use of automation and robotics supporting the ‘Specialised Warehouse and Logistics 4.0’ initiative.
Liu said, “With OMega set to be completed in Q3 2024, it will bolster Malaysia’s logistics and warehousing industry to support growing demand for multinational brand owners and retailers looking to establish their regional distribution centres in Selangor and Malaysia.”
The strategic location and design of ALP Bukit Raja OMega makes it stand out from the other facilities. It has also partnered with major investors such as Malaysia’s largest pension fund, the Employees Provident Fund (EPF), and attracted multinational brands and retailers.
OMega introduces the ‘shared warehouse‘ concept and supports Malaysia’s ‘Logistics 4.0 initiative
OMega is a multi-storey, automation built-in, and technology-integrated warehouse. Inspired by the futuristic concept, OMega introduces a ‘shared warehouse’ structure to offer a flexible rental plan to accommodate industry clients’ business expansion.
It has a world-class shared Automated Storage and Retrieval Systems (AS/RS) at its heart, and separates clients and functions by floors. OMega creates an industry-specific cluster of suppliers and retailers in response to Malaysia’s fast-growing warehousing needs and vigorous development of digitalisation.
OMega will feature 1.8 million square feet in total floor area with an additional 100,000 pallets in the shared automated storage and retrieval system (AS/RS) zone, making it an ideal destination for FMCG, retailers, and e-commerce platforms. A shared warehouse model enables clients with limited resources to afford a customised solution, reduce reliance on human labour, improve operational efficiency, shorten lead time and eliminate human-related errors.
OMega will be able to regulate and reduce the capacity differences between off-season and peak-season of multiple industries, and fully utilise equipment usage and labour force planning to reach maximum economic efficiency.
OMega’s brain ALPOS improves supply chain agility
The brain of OMega is ALPOS, an operating system developed by ALP. ALPOS seamlessly integrates with the client’s warehouse management software (WMS) and manages all the automation within OMega. It not only manages the pallet storage area, but it can also integrate with handling systems for picking, sortation systems, and many others. ALPOS also manages advanced functions such as moving products between clients, termed ‘digital transport.’
ALPOS also features a full reporting suite, allowing operators and management to see exactly what is going on in their operations. The automation solution supports the transformation of labour-intensive supply chains and helps companies tackle the complexity of warehouse management to optimise business processes, gain time and improve cost-efficiency.
Greater focus on analytics provides core competence for retailers, as supply chain agility isthe prerequisite for long-term success in the logistics industry. ALP Executive Vice President (Group Operations Excellence and Regional Business Development) Chris Lower noted, “Whether corporations have an internal logistics department or outsource their logistics, they are increasing their focus on operational flexibility, accuracy, and agility.
“ALP expects corporations will need larger logistics facilities with dense storage to integrate business-to-business (B2B), business-to-consumer (B2C), and multiple retail channel demand, taking advantage of automated equipment and systems to reduce reliance on manpower, improving resilience when facing emergencies, and providing higher service levels to end consumers,” Lower said.
Charting Malaysia’s logistics sector’s path to sustainable development
According to the Malaysia Retail Industry Report published in September 2022, in Q2 2022, the industry recorded an all-time high growth rate of 62.5% in retail sales, compared to Q2 2021.
The retail market is expected to build on this to average 61.7% growth in Q3 2022, proving its great potential and resilience. As the retail market is embracing omnichannel strategies, Malaysia’s logistics players will increasingly require large-scale logistics facilities with flexibility, accuracy, and agility to meet increasing customer demand and future expansions.
The traditional logistics industry lacked long-term and complete solutions resulting in unnecessary waste in the supply chain process. With ALP changing the landscape of the logistics industry in Taiwan and abroad, Malaysian logistics players can remain competitive while accelerating their digital transformations and establishing an upgraded, sustainable business model with the help of groundbreaking smart logistics solutions.